A Q&A With Steve Darwell, Chief Operating Officer at Dincel Structural Walling.
Published 24 August 2023
A veteran within the industry, Steve recently sat down with us to discuss the Permanent Formwork Industry Council (PFIC), and how Dincel Structural Walling remains committed to solving the industry's permanent polymer formwork needs.
Tell us about your role at Dincel and your career highlights to date?
I’ve been in my role as Chief Operating Officer at Dincel since February 2021 overseeing the sales, marketing, operations, and technical teams. Previously, I was at CSR for 18 years, working across various product portfolios including permanent formwork, glass and plasterboard / fibre cement. Prior to that, I spent many years in the packaging industry.
In your role with the Permanent Formwork Industry Council (PFIC), what is at the top of your agenda?
The vision for PFIC is to lead the PVC permanent formwork industry and put it on a solid footing for growth. We are striving to improve the quality of both product and installation of permanent formwork systems to ensure compliance with industry standards. As a board member and chairperson of PFIC, I’m committed to helping the industry work better and more co-operatively to tackle a number of issues that are impacting the growth of the industry. In the last one and a half years since PFIC was incorporated as an association, we have been developing formal standards and training for members, particularly in relation to installation. We also engaged Warrington Fire, a highly regarded testing organisation, to focus on fire compliance when it comes to building with permanent polymer formwork. These external experts have reviewed the Building Code of Australia (BCA) as it applies to permanent polymer formwork, determining how it is a compliant product when installed correctly.
What myth would you like to dispel when it comes to permanent polymer formwork?
There is a general misconception that permanent polymer formwork is non-compliant with the BCA because “it is plastic and therefore it burns”. To be compliant with the BCA a product needs to be either Deemed to Satisfy or pass a comprehensive suite of tests to be considered a Performance Solution and hence compliant. Because of the flame retardants, smoke inhibitors and other additives that are a part of the PVC composition of Dincel’s permanent formwork systems, all compliance requirements are met with flying colours.
What do you believe are the biggest challenges in the Australian building industry today?
One of the biggest challenges, and what the NSW Building Commissioner has focused on, is installation quality. Whilst we do find there are issues with building products, generally it comes back to quality of installation. Dincel has focused on this over the last few years with proactive measures, including the Dincel Academy which has trained more than 800 installers across the country on the correct install methodology for our products. This has been supported by further initiatives that aim to improve building outcomes relating to Dincel permanent polymer formwork installation, including:
facilitating the use of self-compacting concrete (SCC); you don’t need to vibrate the concrete to avoid air voids, so there’s one less concern on site. We’re so confident in its use that we offer an Australian-first Void Free Warranty;
a range of Dincel reinforcement spacers/accessories to ensure the correct position of all vertical reinforcing steel in the permanent formwork when infilling concrete;
investment in installation specialists; we inspect on site to make sure products are installed correctly and offer on-site training as required;
lastly, Dincel has been addressing the issue of waterproofing within basements. We have devised a waterproof system for builds under the water table or where impacted by transient water, helping to prevent water from entering the basement irrespective of ground conditions. When conventional system failures present in basements and water seeps in, it’s hard to find the source of the leak and generally difficult and costly to rectify – and highly disruptive to building occupants. The Dincel Water Stop, when utilised within a system, comes with a zero-leakage warranty for a period of up to 50 years. As we know, land is expensive and more people want to use the subterranean area, including in multi-residential properties. It’s an innovation that’s helping to maximise habitable space, particularly for those living closer to urban centres.
What improvements do you hope to see in the building industry as a whole?
It’s
clear that Australia needs its own dedicated building code for
basements. Practitioners are grappling with how to design basements to a standard, relying on British Codes which don’t take into account mould
and mildew concerns. In addition, a basement wall underground is treated
the same as a façade of a building; there are obviously different
external and internal requirements from a waterproofing and fire point
of view, so confusion reigns. We also need to make building codes more
innovation friendly. In many cases, codes are written around
conventional building methodologies which, at times, make it difficult
for new ideas to prove compliance. For example, permanent polymer
formwork – PVC – when filled with concrete, is a composite building
system which makes it difficult to meet compliance guidelines written
around conventional single material systems. This is one key area that I
believe is stifling innovation and progress in addressing many industry
challenges.
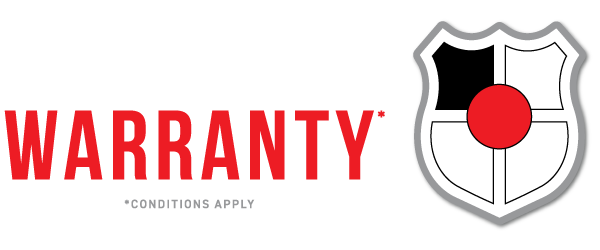
In an Australian first, Dincel is offering a void free warranty when you choose to pour your Dincel Structural Walling with Self-Compacting Concrete and the installation is to Dincel’s specifications.